
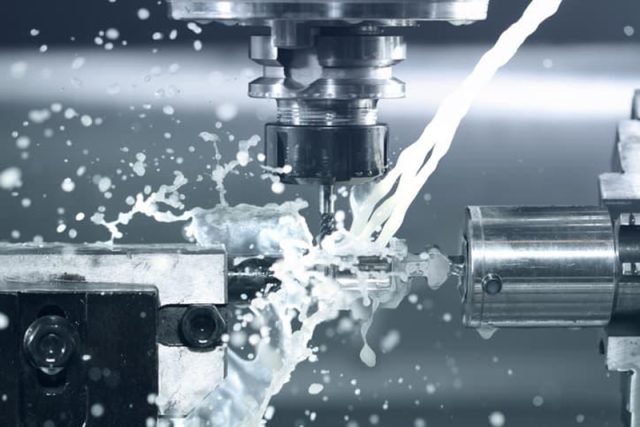
This is what the receiver looked like after the machining was finished.Īfter the 3rd operation was finished, I was able to see if some of the fire control parts would fit. The pic below is the setup I used for the 3rd operation, notice the setup blocks I made for both sides of the receiver to hold it flat and square. This saved alot of time since I didn't have to file so much material out, but for some reason I didn't think about this the first time I made the receivers. The next time I made these receivers I drilled the corners out with a small drill bit. Most companies use a wire EDM (Electrical Discharge Machine), or a broach to complete the mag well, but since I didn't have access to these types of tooling, I had to just machine the mag well, and finish it with a file. Since the endmill will leave a radius in the corner, I will have to go back and use a file to file out the corners so a mag can slide in.
#FLYCUT OR END MILL TO REMOVE MATERIAL FULL#
Since the mag well is so deep, I couldn't get an endmill down to the full depth, so I decided to machine part of the mag well from the top side and finish machining it from the bottom side. I also engraved on this side of the receiver as well.Īt this point I'm able to slide the pistol grip on the receiver a little ways.įor the 3rd operation I machined the fire control area and the part of the magazine (mag) well. I had to make the same rough and finish profiling passes as I did on the 1st operation. This picture is after I used the 3" shell mill to flycut the receiver down to the correct thickness, and then used a carbide endmill to contour around the outside. Here you can see how I made a rough pass around the outside of the receiver to remove most of the extra material.
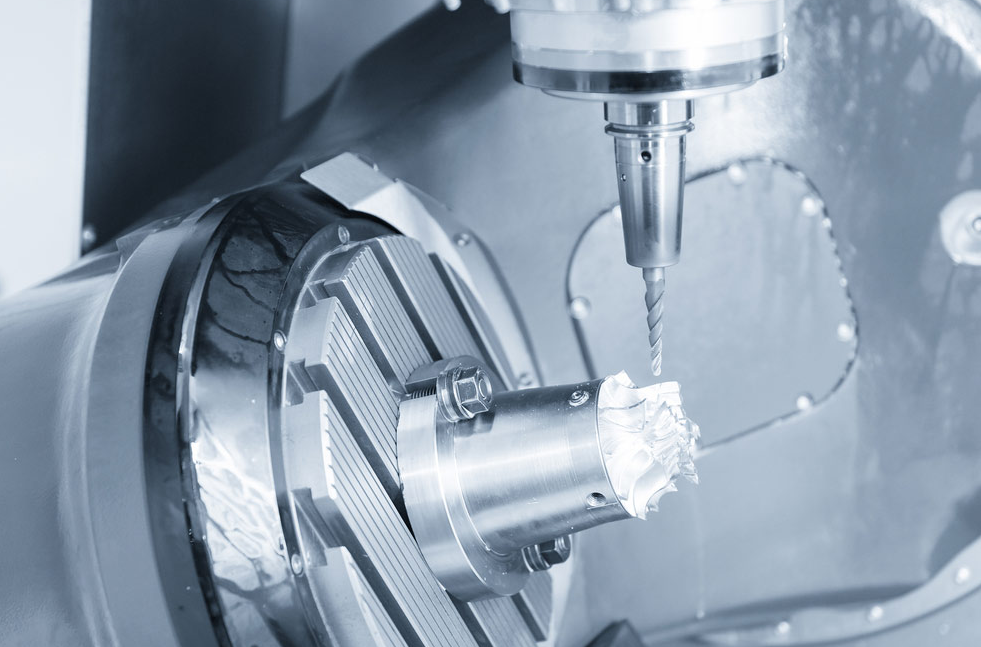
In this picture you can see what the early setup blocks looked like, the current setup blocks are much more advance than this early version. In order to hold the receiver flat and square, I had to design a setup block that the receiver could set on while it was in the vice. Here you can see what it looked like at the start of the 2nd operation. Here's what it looked like after the 1st operation.įor the 2nd operation, I flipped the receiver over and machined the other side to remove the big slab of material. You will see that I engraved AUTO, but this is strictly for looks!!! Since I don't want to spend any time in prison, I never have and never will make any full auto weapons. I also engraved on the side of the receiver. The next step was to do all the detail machining and drilling the holes. Here you can see what the receiver looked like after the finish profiling pass. Machining the receiver the way I did wasn't the most cost effective way, but I wasn't real worried about time, since this was my new hobby. If you had a part that was 7" long, and using a 0.004" step over, it would have to make 1,750 passes. So as you can imagine this process takes a really long time. I started at one end of the receiver and machined across the whole profile stepping over 0.004" each time. You can tell that it's already starting to look like a lower receiver.Īfter the profile was roughed, I then made a finish pass with a 1/4" carbide ball nose endmill. Here you can see the 1/2" carbide ball nose endmill roughing the profile. Here is what the lower receiver looked like at the start of the 1st operation. I cut the 5x2 billets of aluminum, and I was almost ready to start doing some cutting. After I programmed all the tool paths that I wanted the CNC machine to make, I sent the program out to the machining center. Since I already had the solid model of the lower receiver (the CAD part), all that was left was the CAM. CAM is often used along with CAD (Computer Aided Design) and this process is called CAD/CAM.
#FLYCUT OR END MILL TO REMOVE MATERIAL SOFTWARE#
After I had my game plan together, I started programming the lower receiver using a type of computer software called CAM (Computer Aided Machining). I spent many hours coming up with a game plan of how I was going to machine the lower receiver. After I found the solid model file for the AR-15 lower receiver, I knew what I wanted to do could be done. But instead of starting with a forging, I thought I wanted more of a challenge so I started with a block (billet) of aluminum. That got me thinking that I could do the same thing with CNC (Computerized Numerical Control) equipment. He done a great job of showing all the details of his work. He started with a raw forging, which is basically a block of aluminum, but in the shape of lower receiver. Ryan at Roderus Custom Gunworks was working on. I got the idea when I saw the lower receiver forging that Pvt.

The AR-15 lower receiver was the first project that I started.
